As far as the company’s forging technique is concerned, it allows for several heat treatments which consist of sub process of Preliminary process, main process, finishing and cleaning process and inspection process. It is important to perform the heating process before the parts are being casted, rolled and forged. The various heat treatment process includes annealing, normalizing, tempering, Austempering, Hardening, Martempering, Maraging, Surface Hardening, Case-Hardening, Induction Hardening, Flame hardening, Chromising, vacuum heat treatment and Boronizing.
After the hardening process, next comes the tempering process that is performed for enhancing friction resistance and also to provide strength, elasticity and toughness to the material. In this process, the steel is heated at a rate above critical temperature. While the hypereutectoid steel is heated at a temperature of 30 to 40 degree Celsius more than AC3 temperature, hypereutectoid steel is heated at the same temperature more than AC1 temperature. In case of high-speed steel and alloy steel, the heating is done between 1100to 1300 degree Celsius. For conducting the heating process, there are requirements carbon content and alloys, homogeneity of austenite, grain size, the required state and rate of quenching, and surface condition. With the help of hardening process, steel hardness and friction resistance is increased and steel toughness is also enhanced.
Another heat treatment process as mentioned above is the annealing process. In this phase, the steel is heated till austenite stage and temperature is maintained for some time. In this stage, the steel is heated at a temperature between 30 to 50 degree Celsius, then maintained for 2 hours and then finally cooled down at room temperature. This process is essential for manufacturing stable steel structure, refined and linear structure, reduce toughness, increase ability of machines, relieve stress, and also to eradicate gas from the steel for increasing chemical, electrical, and mechanical properties. Some of the process under annealing includes:uniform structure, for achieving better good weld structure, and for enhancing steel properties.
- Isothermal Annealing
- Full Annealing
- Process Annealing
- Stress Relieving
- Diffusion Annealing
- Spherodise Annealing
In the normalising phase, the steel component is heated between 30 to 40 degree Celsius more than AC1 and AC3 temperature. This process is extremely for the company to follow in order to increase the ability of the machine, and also the strength of the castings. It also helps in removing stress that arises due to forging, bending and hammering, thereby bringing uniformity in structure and relieving stress. With the help of this process, yield point is increased, along with tensile and impact strength. This process is usually followed for huge castings and forgings, for refining grain size, for achieving uniform structure, for achieving better good weld structure, and for enhancing steel properties.
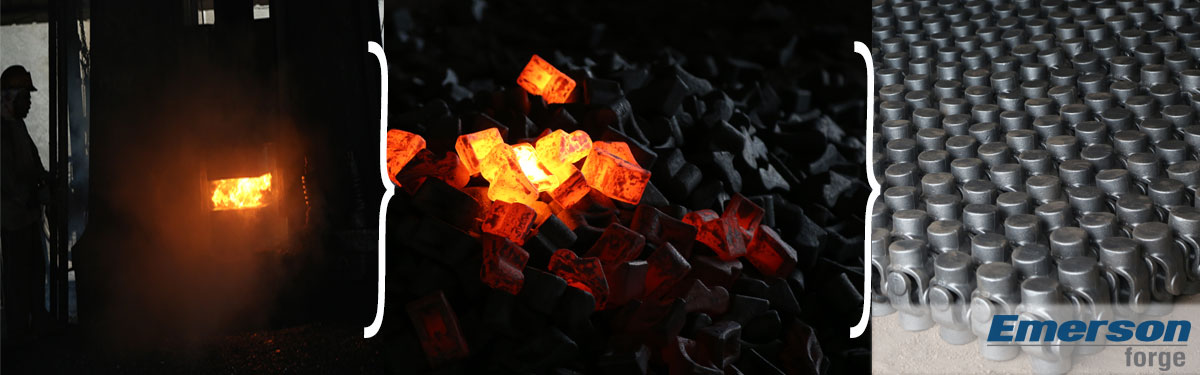
The last treatment process is the tempering process. In this process, the steel is heated, but not above the critical temperature, and in the process, the steel acquires its mechanical processes and also internal stress is removed. The stress that is generated in the process is relieved when the same temperature is maintained for 15 to 30 minutes. In case tempering is done at a temperaturebetween 150 to 250 degree Celsius, then the steel toughness and strength is increased, along with friction resistance. The medium and advisable temperature is 350 to 500 degree Celsius, where toughness and required elasticity is achieved.